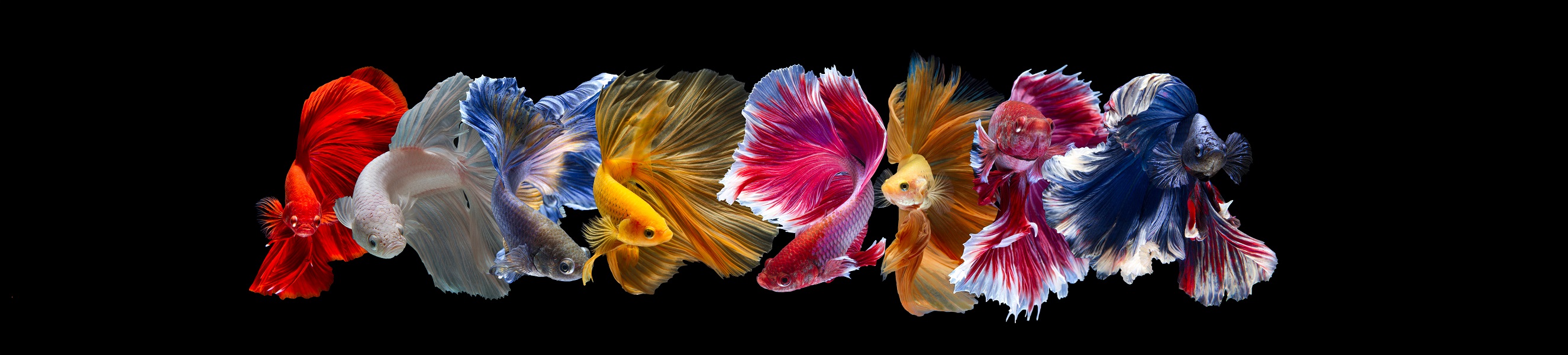
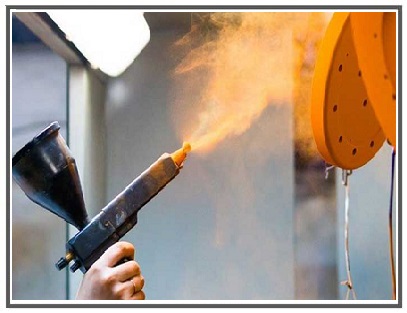
why powder coatings
Category: PowderType: Article
1/20/2022
Why powder paint
Since the introduction of powder paint in the 1960s in North America, these paints have become very popular in different countries. These colors cover about 15% of the industrial colors market and are used in a wide range of products. Today, different companies have a special look at powder paints, which is due to high quality, more durability, more efficiency and compatibility with the environment. Decorative powder coatings are available in an unlimited range of colors and textures, the advancement of technology has improved their practical features.
How powder coatings work
Powder paint is made on the basis of a polymer resin system that is combined with pigments and other additives and modifiers. These materials are mixed together and melted, then cooled and become a uniform powder. During a process, electrostatic powder paints are sprayed on a metal substrate, in such a way that a spray gun is used, which applies an electrostatic charge on the powder particles and then the part is absorbed.
After applying the powder coating, the parts are put into a baking oven, which increases the heat and the coating shows a chemical reaction and the molecular chain becomes longer, which causes a strong connection between the particles. These molecular chains are very resistant to breaking and this type of spraying is the most common method of applying powder colors. Powder coatings can also be applied on non-metallic surfaces such as plastic and MDF.
Sometimes powder coatings are applied using a fluid bed. The parts are preheated and immersed in a liquid powder tank, as a result the powder melts and flows on the part.
Excellent coverage
Today's consumers expect more, they want products that are durable, attractive and long lasting. They know the protection level of powder paints and this is the coverage they want from manufacturers. Powder coatings cover a wide range of decorative and special industries. Compared to other coatings, powder coated surfaces are more resistant to chipping, scratching, fading, and corrosion. The color options are unlimited. And the coating with different glosses and metallic and transparent surfaces is easily available. Paint texture can also include different options such as smooth surfaces, wrinkled or matte coatings designed to hide surface imperfections.
Durability of powder paint
Powder coating is a high-quality coating found on thousands of products you come into contact with every day. Powder paint protects the toughest machines and household appliances that you use daily. Powder paints offer a more beautiful surface despite their high durability compared to liquid paints. Powder coated products are more resistant to degradation due to impact, moisture, chemicals, UV rays and other extreme weather conditions. This in turn reduces the risk of scratches, scuffs, wear, corrosion, fading and other wear and tear problems.
Compatibility with the environment
Powder coatings are highly compatible with the environment. While liquid coatings contain solvents that contain pollutants known as volatile organic compounds (VOCs, powder coatings are solvent-free) and therefore release small amounts of VOCs into the atmosphere. Costly waste storage and disposal is not required. In addition, powder left over from spraying is recycled and reused in the cabin and unused powder, which virtually eliminates the waste normally found in liquid paints.
High efficiency
By using powder coating, all the problems you face after using liquid paints are eliminated, such as smudging or dripping paint. No drying time is required, so powder coating production lines run more efficiently than standard paint lines. Parts can also be coated in an automated process. Using the right application equipment, materials and recovery methods, powder utilization efficiencies of 95% to 98% are easily achievable.
Cost-effectiveness
In addition to high performance, the use of these coatings saves money due to the simple process that powder coating provides. Parts can be moved closer together on the conveyor and move through the production line faster, reducing costs per unit. This production efficiency is economically useful for both the part manufacturer and the customer.
Energy storage
The energy required for powder coating furnaces is less and thus helps to reduce energy consumption. Whereas ovens that bake solvent-based coatings must heat and vent large volumes of air to protect the part from the vapors present.