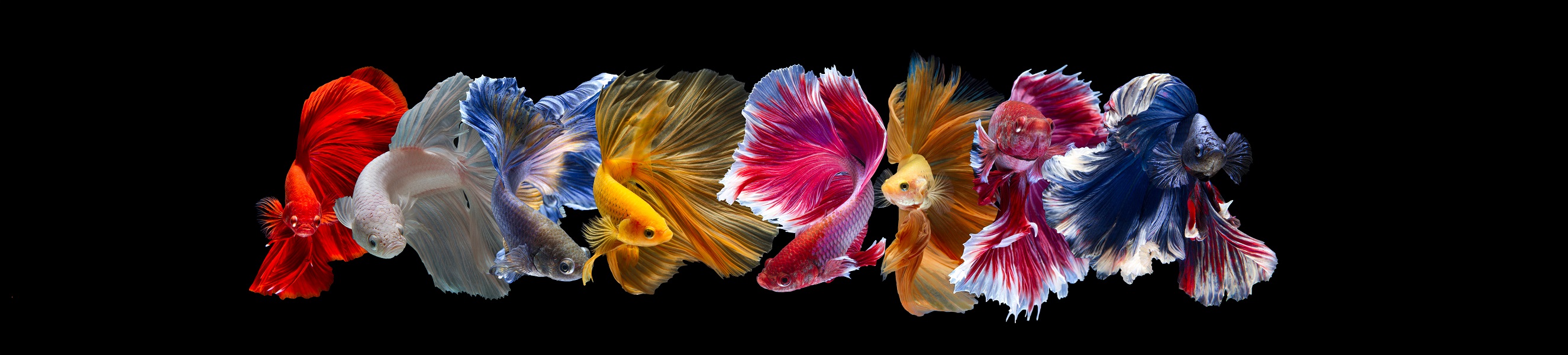
راهنمای عیب یابی - پوشش فام
دلیل
1- نگهداری و حمل و نقل کارتن های رنگ در شرایط نا مساعد گرم و مرطوب(دما و رطوبت مجاز مندرج روی کارتن)
راه حل
1-1- از حمل و نگهداری در شرایط گرم و مرطوب خودداری شود با رعایت مندرجات کارتن
1-2- کلوخه ها در صورت امکان با الک 90-100 سرند و با فشار هوای تمیز در مخزن معلق شود
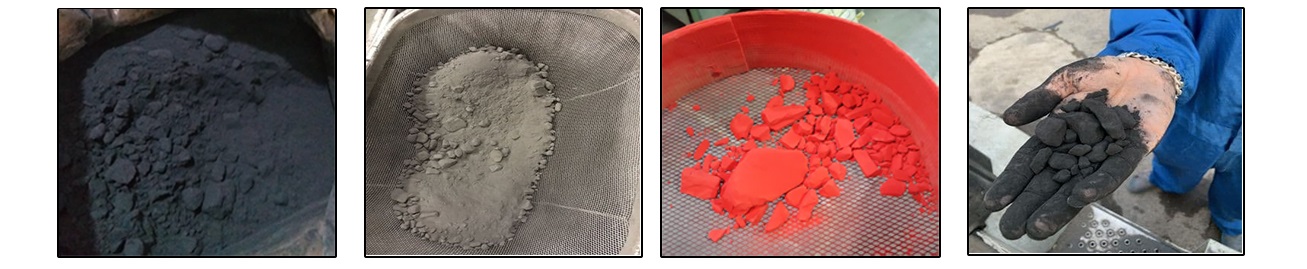
دلیل
1- کافی نبودن فشار هوای زیر مخزن
2- مسدود شدن منافذ هوای صفحه فلودایز زیر مخزن
3-رطوبت پودر
4- گرمای محیط
5- تراکم پودر کف مخزن
راه حل
1-1- فشار هوای مخزن افزایش یابد
2-1- پاکسازی مخزن و منافذ صفحه فلودایز زیر مخزن
3-1- سرند کردن پودر (هوا دهی)
4-1- خنک کردن محیط خط رنگ
5-1- کاهش حجم پودر مخزن و هم زدن رنگ جهت معلق شدن پودر
دلیل
1- پر کردن بیش از حد مخزن رنگ
2- آلودگی آب و روغن در هوای فشرده کمپرسور
3- گرمای محیط خط رنگ
4- نرم بودن ذرات پودر
راه حل
1-1- کاهش حجم رنگ مخزن به میزان تا یک چهارم
2-1- فیلترهای هوا و روغن کمپرسور کنترل و پاکسازی شود
3-1- کاهش دمای محیط رنگ
4-1- افزایش رنگ نو به بازیافت
دلیل
1- بالا بودن فشار هوای زیر مخزن
2- پر کردن بیش از حد مخزن رنگ
3- نرم بودن پودر از نظر دانه بندی
راه حل
1-1- کاهش فشار هوای زیر مخزن
2-1- کاهش حجم رنگ تا قطع شدن سرریز رنگ
3-1- در صورت نو بودن رنگ با شرکت سازنده تماس گرفته شود.
دلیل
1- باز بودن غیر ضروری و بیش ازحد دهانه های ورود و خروج کابین پاشش
2- مسدود شدن فیلتر هواکش و فیلترنهایی (بک فیلتر)
3- محل و طراحی نامناسب شکل کابین پاشش
راه حل
1-1- بستن و تنظیم دهانه های ورود و خروج قطعات به کابین
2-1- افزایش مکش هوای کابین بوسیله پاکسازی فیلترهای مربوطه
3-1- اصلاح محل و شکل کابین در صورت امکان و یا کاهش فشار پودر خروجی از تفنگی ها
دلیل
1- بالا بودن غلظت پودر نسبت به هوای پاشش
2- فرسودگی قطعات دستگاه پاشش
3- طولانی بودن و یا پیچ خوردگی شیلنگ های پاشش
4- دانه بندی نرم پودر
راه حل
1-1- کاهش فشار رنگ خروجی از تفنگی و افزایش فشار هوای پاشش
2-1- کنترل و تعویض قطعات فرسوده تفنگی پاشش
3-1- کنترل و تعویض شیلنگ های پاشش
4-1- افزایش فشارباد جوشش(فلودایز) و کاهش سطح رنگ در مخزن تغذیه
دلیل
مشکل الکتریکی خط پاشش (اتصالات – ولتاژ پایین)
فاصله زیاد تفنگی
چیدمان متراکم قطعات در کنار هم
درشت بودن دانه بندی رنگ
سرعت بالای خط نقاله یا اپراتور پاشش
راه حل
برقراری اتصالات و تمیز کاری گره ها، تنظیم و افزایش ولتاژ تفنگی
رعایت فاصله لازم تفنگی از قطعه
افزایش فاصله چیدمان قطعات در گیره ها
کنترل دانه بندی و افزودن بازیافت
کاهش سرعت خط نقاله و پاشش اپراتور
دلیل
نسبت خروجی پودر بالاست
فاصله تفنگی با قطعه کم است
سرعت خط پایین است
ولتاژ خط بالاست
راه حل
" کاهش نسبت پودر و افزایش هوای پاشش
تنظیم فاصله تفنگی"
بالا بردن سرعت خط پاشش
کنترل قطعات الکتریکی و فیوزهای دستگاه پاشش جهت کاهش ولتاژ
دلیل
بالا بودن ولتاژ تفنگی
پایین بودن غلظت پودر خروجی
عدم اتصالات
زیاد بودن بازیافت پودر
زاویه و فاصله نامناسب تفنگی
نامناسب بودن نوع رنگ کرونا برای قطعات دارای پیچیدگی زیاد
راه حل
کاهش ولتاژ تفنگی
کاهش فشار هوای تفنگی و افزایش خروجی پودر
کنترل اتصالات و پاکسازی گیره ها
افزودن رنگ نو
تنظیم فاصله و زاویه پاشش تفنگی
تماس با شرکت تولیدی برای تولید رنگ ترایبو جهت قطعات پیچیده
دلیل
مقدار متالیک بیش از حد است
پودر مرطوب است
مقدار رنگ بازیافت زیاد است
ضعیف بودن ارت
راه حل
تماس با شرکت کننده رنگ
تمیز کردن تمام تجهیزات و استفاده از پودر نو
چک کردن نسبت رنگ بازیافت به رنگ نو
کنترل اتصالات ارت
دلیل
بالا بودن ضخامت لایه رنگ
فرار رنگ به لبه های کار
طولانی بودن فرآیند پخت
ریزش پودر و تجمع در لبه های پایین کار
راه حل
کاهش خروجی پودر تفنگی و لایه رنگ
بررسی وضعیت ارت و کاهش ولتاژ
بررسی وضعیت کوره وکاهش زمان پخت
استفاده از نازل مناسب پاشش تفنگی
دلیل
آلودگی پودر (ترکیب رنگ با رنگی دیگر در سیستم پاشش)
حرارت دادن سریع و بالا در زمان پخت
آلودگی آب و روغن درهوای کمپرسور
راه حل
تخلیه و پاکسازی سیستم پاشش و مخزن از رنگ آلوده
کاهش دمای ورودی کوره
بررسی هوای کمپرسور درمحل اتصال به پاشش و پاکسازی فیلتر و شلنگهای مربوطه
دلیل
پخت ناقص در کوره
ضخامت بالای قطعه
راه حل
افزایش دما و زمان اقامت قطعه در کوره
" انجام عملیات پیش گرم روی قطعه قبل از پاشش رنگ
(در بعضی موارد با پخت مجدد براقیت مقداری کاهش می یابد)"
دلیل
الودگی کابین وسیستم ومخزن پاشش با رنگ قبلی
احتمال فاسد بودن رنگ تازه
بالا بودن دمای پخت
راه حل
پاکسازی کامل سیستم پاشش و مخزن
تماس و مشاوره با شرکت تولیدی رنگ
کاهش دمای کوره
دلیل
نازک بودن لایه رنگ
فرسودگی دستگاه پاشش
ضعیف و یا قطع بودن اتصالات الکتریکی
اشکال در فرمولاسیون پودر
راه حل
افزایش لایه رنگ اعمال شده
تعویض قطعات دستگاه پاشش
بررسی قابلیت های ولتاژ پاشش و ارت
تماس و مشاوره با شرکت تولیدی رنگ
دلیل
ضخامت پایین لایه رنگ
فرسودگی و نقص دستگاه پاشش
مشکل در اتصال ارت
آلودگی شدید هوای کمپرسور به آب و روغن
راه حل
افزایش ضخامت لایه رنگ
تعمیر و تعویض قطعات دستگاه پاشش
بررسی اتصال ارت و تمیزکاری گیره ها
کنترل، پاکسازی و تعویض فیلترهای کمپرسور و شلنگ های مربوطه
دلیل
درشتی ذرات پودر رنگ
نوسان ولتاژ دستگاه پاشش بعلت فرسودگی
کم بودن فاصله تفنگی با قطعه
توقف زیاد قطعه در معرض پاشش پودر
راه حل
سرند کردن پودر با الک ریز تر از 100 و تماس با شرکت تولیدی رنگ
کنترل ولتاژ و تعویض قطعات تفنگی
حفظ فاصله مناسب تفنگی و یا کاهش فشار باد خروجی پاشش
افزایش سرعت خط و اپراتور پاشش
دلیل
بالا بودن دما و زمان پخت
اختلاط رنگ پودری با رنگ مات
تغییر فرمولاسیون رنگ
راه حل
کاهش فرآیند دما و زمان پخت
پاکسازی سیستم پاشش از رنگ قبلی و مخلوط
تماس و مشاوره با شرکت تولیدی رنگ
دلیل
پایین بودن دمای کوره
اختلاط پودر با رنگ صاف در مخزن
انقضای تاریخ مصرف رنگ
ضخامت بالای قطعه و لایه پوشش
نگهداری رنگ در شرایط غیر استاندارد
راه حل
تنظیم و افزایش دمای کوره
پاکسازی خط پاشش از رنگ غیر چرمی
توجه به تاریخ انقضای مندرج در بسته بندی
انجام عملیات پیش گرم روی قطعه
کنترل وضعیت محل نگهداری رنگ از لحاظ رطوبت
دلیل
ضخامت بالای پوشش لایه رنگ
پخت ناقص رنگ
آلودگی سطح قطعه به دلیل شستشوی ناقص
راه حل
ضخامت استاندارد لایه رنگ رعایت شود
دما و زمان پخت با توجه به مندرجات بسته بندی رعایت شود
مراحل شستشوی قطعه بخصوص چربی زدایی کنترل شود
دلیل
تاثیر مستقیم عوامل محیطی و تابش نور ماوراء بنفش خورشید
راه حل
جهت پوشش کلیه قطعات مورد استفاده در معرض نور خورشید از رنگهای پایه پلی استر PE استفاده و از کاربرد رنگهای هیبرید(MX اپوکسی پلی استر) خودداری شود
دلیل
آلودگی پودر با مواد نامنطبق و ناسازگار
شستشو و چربی گیری ناقص و نامناسب
وجود آلودگی آب و روغن در هوای کمپرسور
بالا بودن ضخامت لایه رنگ
مرطوب بودن پودر رنگ
راه حل
پاکسازی کامل سیستم پاشش از رنگ آلوده
کنترل فرآیند شستشو و چربی گیری قطعات
کنترل هوای خروجی کمپرسور از نظر آلودگی آب و روغن
کاهش ضخامت لایه پودر رنگ
سرند کردن پودر و کنترل وضعیت نگهداری رنگ
دلیل
بالا رفتن سریع دما در ورودی کوره
کم و یا زیاد بودن لایه رنگ
پایین بودن دمای پخت رنگ
عدم اتصال ارت
مرطوب بودن پودر رنگ
راه حل
کاهش دمای ورودی کوره با تنظیم پرده هوا
تنظیم ضخامت لایه رنگ
توجه به مندرجات پخت رنگ روی بسته بندی
کاهش دمای محیط خط و قطعه قبل از پاشش
بررسی اتصال ارت
تماس و مشاوره با شرکت تولیدی رنگ
دلیل
اختلاط رنگ با مواد غیر و سمباده ای
آلودگی آب شستشو و چربی گیری ناقص
آلودگی گرد و غبار محیطی
وجود آب و روغن در هوای کمپرسور
نازک بودن لایه پوشش نهایی
راه حل
تخلیه و پاکسازی سیستم پاشش
تعویض و کنترل مرتب آب و مواد شستشو
رفع گرد و غبار محیط خط پاشش
کنترل هوای کمپرسور در محل اتصال به پاشش
افزایش ضخامت لایه رنگ
دلیل
- نوسان شدید ولتاژ دستگاه پاشش
- اتصال ناقص ارت
- پیچیدگی قطعه
- آلیاژ و جنس فلز قطعه (زاماک)
راه حل
- کاهش کیلو ولت دستگاه پاشش در حد امکان و تعمیر دستگاه در اسرع وقت
- بررسی اتصال ارت و تمیزی گیره ها
- امکان استفاده از رنگ ترایبو در مشاوره با شرکت تولیدی رنگ
- بررسی آلیاژ در تماس با سازنده دستگاه
دلیل
ضخامت بسیار بالای لایه رنگ
رطوبت پودر
اختلاط پودر با مواد ناسازگار
زبری زیاد سطح قطعه
تغییر در فرآیند تولید پودر
راه حل
کاهش ضخامت لایه پودر
سرند کردن و هوادهی پودر و کاهش دمای محیط خط
پاکسازی مجدد خط پاشش
زیر سازی و آماده کردن قطعه اصلاح شود
تماس و مشاوره با شرکت تولیدی رنگ
دلیل
آلودگی سطح قطعه بدلیل شستشو و پاکسازی ناقص
پخت ناقص رنگ
ضخامت زیاد لایه رنگ
راه حل
کنترل مراحل شستشو با بررسی و مشاهده زیر لایه پوسته شده
افزایش فرآیند زمان و دمای پخت
کاهش ضخامت لایه رنگ در حد استاندارد
دلیل
پایین بودن دمای کوره در زمان ورود
اختلاط و آلودگی با رنگ غیر چکشی
ضخامت فلز قطعه بیش از 4 میل
انقضا تاریخ مصرف
نگهداری نامناسب پودر
بالا بودن مقدار بازیافت رنگ
راه حل
رنگهای چکشی در ورود به کوره با دمای بالای 130 درجه شوک بگیرند
پاکسازی خط پاشش از رنگ غیر چکشی
انجام عملیات پیش گرم روی قطعه
کنترل و بررسی محل نگهداری پودر
کاهش مقدار بازیافت و جایگزینی با رنگ تازه
دلیل
سایش و لمس توسط عوامل انسانی و عوامل محیطی
راه حل
استفاده از لایه محافظ لاک ورنی پودری بر روی پوشش نهایی پس از پخت
دلیل
عدم اتصال ارت علت اصلی و اساسی مشکلات در چسبندگی پودر و پوشش و بافت نهایی رنگ است.
راه حل
تمیزکاری نقاط اتصال گیره ها و نقاله بطور مرتب
اطمینان از برقراری ارت بر روی قطعه با اهم متر
اتصال قوی زمین با اتصال کابل
دلیل
آلودگی هوای کمپرسور از دلایل اصلی کاهش براقیت, حفره و دانه زدن پوشش, کاهش کیفیت پودر و پاشش, کلوخه شدن ,افزایش مصرف رنگ و فرسودگی قطعات تفنگی پاشش است
راه حل
نصب فیلتر روغن گیر و درایر رطوبت گیر در نزدیکترین نقطه به دستگاه پاشش روی مسیر شلنگ باد
کنترل مداوم هوای ورودی به پاشش از طریق استوانه شیشه ای فیلتر زیر دستگاه
اسپری کردن باد خروجی روی آیینه